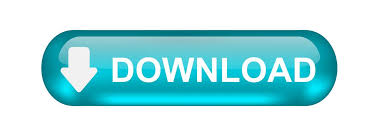
The involute worm gear may be mounted on cheaper bearings. Axial thrust in the spur gear is eliminated under such a scenario. The same is also valid with respect to two-starts worm gear pairs. Orthogonal worm gear pairs may be designed so as to engage a spur gear in mesh with a mating involute worm under a right shaft angle in the worm gear pair. The discussed approach for the calculation of the design parameters of an involute worm for a right-angle mesh with an involute spur gear also was used in designing hobs for cutting spur and helical cluster gears, ,, and others. The thicker threads in the worm depicted in Figure 6 are stronger, and - what is also of critical importance for highly-rotating worms - provide significantly better heat removal from the friction zone between the worm threads and the gear tooth flanks. The first is much smaller than the second (that is, an inequality t o.w t o.w, measured on the bottom-land and outer cylinders correspondingly). This is made clear from a comparison of the thickness of the worm top land, t o.w, and of the space width, w f.w, in the bottom land. Later on, width of the space between the worm threads was enlarged, and in this way, an additional room was created in order to get the worm engaged in mesh with a spur gear. It is right point to stress here that originally shown in the Figure 2 worm was designed to be engaged in mesh with a helical gear. Here, a “worm-to-spur gear” gear pair with a right shaft angle is shown ( Σ = 90°). An example of such a gear pair is depicted in Figure 2. It should be mentioned here that right-angle gear pairs with an involute worm engaged in mesh with a spur involute gear are known. The replacement of a helical gear with an equivalent spur gear is beneficial as the axial thrust pointed along the spur gear axis of rotation in this case is eliminated, and the shaft can be mounted on bearings of a cheaper design. Manufactured this way, the gears get cheaper. Under such a scenario, the spur gear is manufactured using a technology adopted easier in production of plastic gears or PM gears. However, in particular applications, it is preferred to have worm gearings (a) with a shaft angle equal to a right angle, and (b) with a spur (not helical) gear in mesh with a mating worm. Figure 1: An orthogonal “worm-to-helical gear” gear pair. It is evident that the shaft angle in this particular application is not a right angle ( Σ ≠ 90°). The shaft angle, Σ, in this case equals Σ = 90° – ψ w. In “worm-to-spur gear” mesh, it is a common and well-established practice to set the worm in relation to a mating spur gear at an angle that corresponds to the worm pitch helix angle, ψ w. For example, spur gears are easier in production compared to worm gears, helical gears, double-helical and/or herring-bone gears, gears with circular arc geometry in the lengthwise direction of the gear tooth, and so forth. Unfortunately, not every kind of gears can be made of plastic or use conventional methods adopted in powder-metal industry. In many cases, gears of regular design can be successfully replaced either by plastic gears, or by PM gears that are usually less expensive and of a higher quality. In recent decades, plastic gears, as well as powder-metal gears (PM gears) got an extensive application in a variety of industries. Certain advantages of gearing theory accomplishments can be taken in order to combine the benefits of plastic-gear technology, and of powder-metal technology, with benefits of particular designs of worm-gear pairs. Gears of this kind are better suited for manufacturing, and, thus, they can be cheaper in production, while gears of other kinds are inconvenient in production, which makes them costlier. The technology used in production of plastic gears, as well as powder-metal technology, imposes certain constraints on the design parameters of a worm and of a mating gear. T his article deals with worm gearings in cases when the worm-gear pair is composed either of plastic or of powder-metal made components.
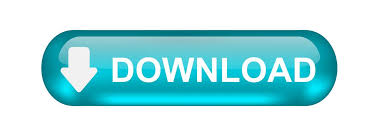